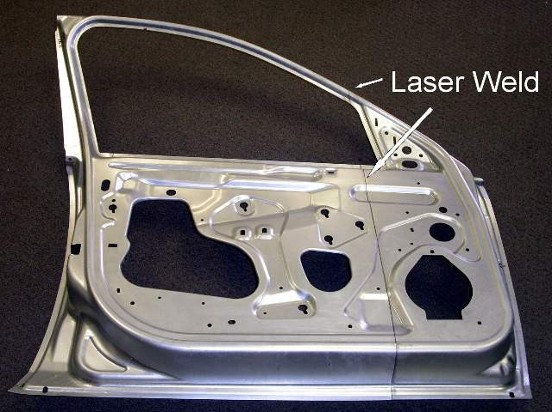
Laser-welded blanks are typically composed of different
types and thickness of steel, which are welded together
into one piece. The piece is then stamped into shape as a
single unit such as an automotive door or body side panel.
Using this method, manufacturers add strength to
parts where it is needed, reduce weight, improve
performance, better corrosion protection by the elimination
of overlapped joints, and reduce costs due to the reduction
of dies, presses, etc. due to fewer production steps.

Blanks are welded together with a linear weld
(upper right photo),
a curve-linear (left photo), or non-linear (not shown).
Our facility is spacious with ample room for inventory segregation, inspection, and process development. Our building features
a delivery bay area and a pick up bay area with sufficient materials handling equipment for
production volumes.
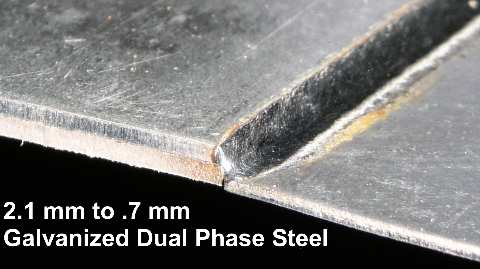
Weight Reduction
Cost Savings
Tooling Reduction
Increased Structural Integrity
|